Listen to this article
|
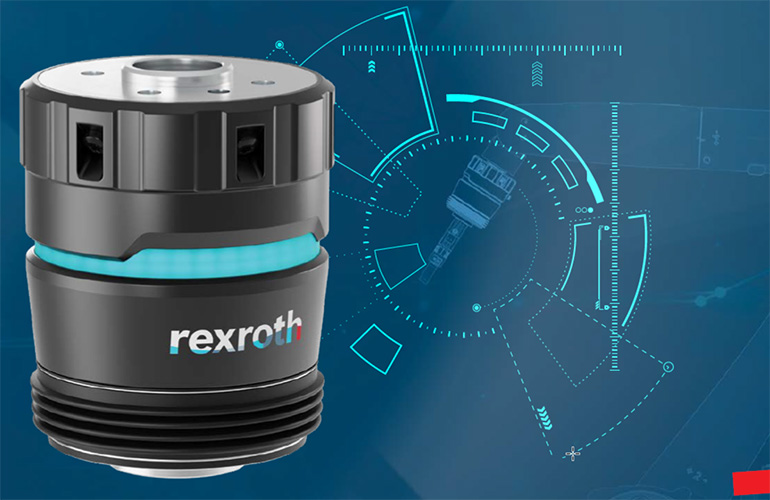
Bosch Rexroth’s Smart Flex Effector its in between the robot and its gripper to make it more flexible and precise. | Source: Bosch Rexroth
In 2022, there were 3.9 million operational robots in the world, an all-time high, according to the International Federation of Robotics. Bosch Rexroth said it expects that number to grow in the coming years as new innovations make it possible for robots to do more tasks more successfully.
The Buchanan, Mich.-based company creates intelligent systems for factory automation, mobile and machining applications, and engineering. It said it hopes to help the industry keep up with rising demand by making robots more flexible and easier to use.
Brad Klippstein, a product manager at Bosch, gave insight into the company’s Smart Flex Effector. This end effector, which sits between the robot and its gripper, gives a robot tactile feedback. This allows a robot to know when it’s touching an object and how to get into position to best pick that object.
“We’ve had vision systems for robotics for a number of years,” Klippstein told The Robot Report. “Now, we’re adding tactile sensing to that process to increase accuracy, increase repeatability and process transparency, and do some of these operations that were incredibly difficult or impossible before.”
Learn from Agility Robotics, Amazon, Disney, Teradyne and many more.
Bosch Rexroth makes industrial arms more adaptable
Robots, particularly large industrial robots, can be inflexible and difficult to train on new tasks, noted Bosch Rexroth. Robots used in picking processes typically have “teach positions,” which are ideal positions for the robot and the item it’s picking to be in.
Industrial robots will typically pick the same item over and over again, so when the item or the robot is slightly off position, the robot may struggle to complete the task.
“Lots of things can happen to make that teach position be a little bit misaligned or off position,” said Klippstein. “The Smart Flex Effector gives you the ability to feel the environment.”
“So now I don’t have to know the exact position of an object or location,” he added. “I can get somewhat close and then have the Smart Flex Effector tell me exactly where to go based on tactile sensing or touch.”
While vision systems can provide important feedback for robots, tactile feedback adds a new level of flexibility to robots, asserted Bosch Rexroth.
“As soon as the robot touches the workpiece you get that feeling, that feedback. And that can tell the robot that it’s in position,” explained Klippstein. “For high picking and placing operations, we don’t need to be exact. With all of these teach positions we can get somewhat close and the smart flex effector adds flexibility to that process so that you don’t have to reteach that position each and every time.”
“So if we know that the position is off half a millimeter in the X direction, three-quarters of a millimeter in the Y direction, and 2.5 degrees about the X-Y axis, and we know all of those dimensions immediately, we can send that information back to the robot,” he said. “Then it knows the exact position to correct.”
Designing a tool that can work with any robot, in various use cases
The Smart Flex Effector can work with any robot or gripper, according to Bosch Rexroth. The system simply uses an adapter plate that allows end-users to connect any equipment. It’s also designed to benefit robots in a variety of use cases, not just picking.
Klippstein said Bosch’s end effector is used in assembly operations, the electronics industry, machine tending, welding, and various other industrial applications. It wasn’t easy for the company’s team to create something that can work in so many scenarios.
“We needed to make something that was compact, durable, and that, of course, performed this operation by taking in all of this data,” said Klippstein. “And by the way, this data is six degrees of freedom, or six degrees of rotation about the robots. We needed to be able to provide compensation for each one of those six axes in almost real-time, because we don’t want to slow down operation.”
“So we needed to quickly determine the offset, the positional deviation from where that robot currently is in all six degrees, and then quickly send that result back to the robot control so that it can make a compensation move,” he said.
“The engineering challenge was we needed to obtain this information,” Klippstein said. “So how do we even get that?”
“We need to be able to process that and determine the position, not just the force or the torque or anything like that,” he said. “You program a robot with position, so it’s very easy to tell the robot how far to move if you know the exact degree or the millimeter that it needs to move to. We get that information, send it to the robot, and it knows the exact position to move to for the correct movement or to find the nominal position.”
While the tool has primarily been used in six-axis robots, it can be implemented in any robot that needs more flexibility and accuracy, Klippstein claimed.
Why flexibility is necessary for the industry as a whole
As robots become more and more mainstream, flexibility and ease of implementation have become increasingly important topics for the industry.
“As far as trends, I would say it’s making [end effectors] easy to implement into whatever robot the customer wants to use,” Klippstein said. “As far as establishing the communication, making it really easy to program from that teach pendant is a really big trend and something that is necessary to allow customers to quickly implement the solution.”
Klippstein also said that recent advances in artificial intelligence should help end-of-arm tooling like the Smart Flex Effector become more accurate over time.
“[More information] gives you insights to what is actually going on so that you can either program around it, or have a better understanding of that process in general, and find new ways to implement that solution or that process in other areas as well,” Klippstein said.
Tell Us What You Think!