Listen to this article
|
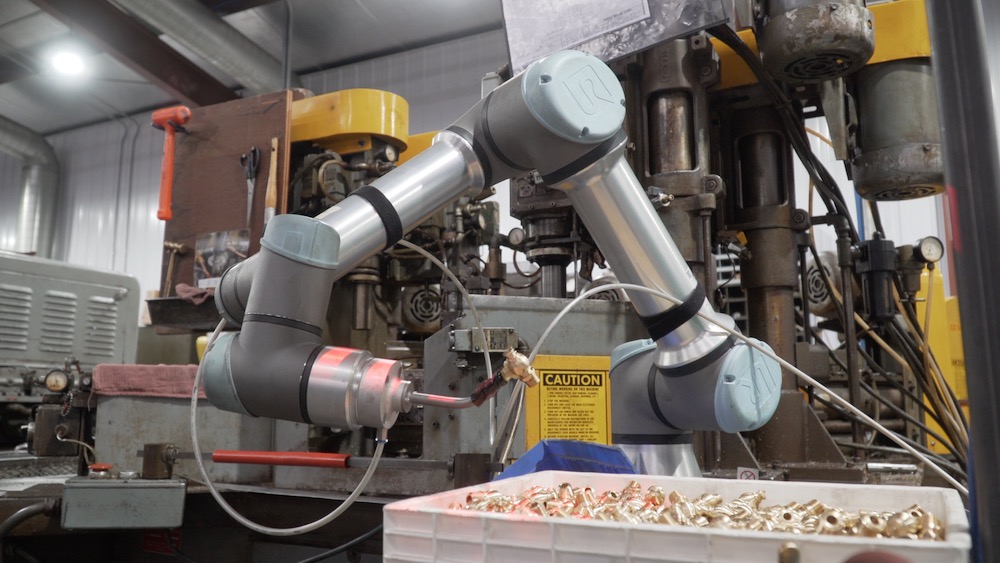
ActiNav picking parts from a deep bin for Flywheel Supply in Iowa. | Photo Credit: Universal Robots
Universal Robots (UR) selected four U.S.-based systems integrators to deploy its ActiNav next-generation machine loading solution. Launched in April 2020, ActiNav combines real-time autonomous motion control, UR cobots, vision and sensor systems to automate bin picking tasks or machine tending applications.
The systems integrators already selected are:
- Eckhart (Michigan)
- Integro Technologies (North Carolina)
- Southwestern Production Technology Solutions (Texas)
- Cross Company (North Carolina)
UR said more ActiNav integrators in the U.S. and Canada will be announced before the end of Q2 2021.
“Our selection process focused on integrators with expertise in both vision and robotics, delivering superior value, and on time/on budget projects for customers,” said Bryan Bird, regional sales director for Universal Robots’ North America division.
The selected systems integrators have all been provisioned with in-house demo units, enabling them to develop proofs of concepts for customers in their region.
“Integrating ActiNav into a machining cell is where the expertise of the right systems integrator really shines,” said Bird. “Our integrators will be able to quickly handle all peripheral requirements such as integration with safety sensors, machine interfaces, end-of-arm tooling and other components that all need to work together.”
ActiNav has been deployed with numerous manufacturers across North America, who were seeking a simple solution to a complex problem. One of them is Flywheel Supply in Iowa. A UR5 cobot picks parts from a deep bin and places them in the jaws of a machine that indexes to multiple stations to perform tasks such as drilling, chamfering, and internal and external threading. ActiNav will process as many as 1,500 different part numbers, so it must be quickly programmable to pick parts of different shapes, sizes, and weights.
“The only way that made sense for us to put a robot on a machine tending application was to be able to do randomized bin picking,” explained Zach Northway, co-owner and lead project engineer at Flywheel Supply. “The cycle times on the machine are so short that if an operator has to stand there and line parts up in an organized fashion for a robot to pick them in a traditional sense, it would defeat the entire purpose of using the robot to begin with, because your operator is still standing there.”
“The biggest advantage to ActiNav is that it can take randomization of parts being dumped in a bin, and as the bin gets low, a person can just come by and dump some more into the bin and it will keep picking parts,” said Northway. “It doesn’t have to be reset, recalibrated—anything. It notices the bin amount changed and it keeps on going.”
To learn more about Universal Robots’ ActiNav, watch this on-demand webinar called “Next-Generation Cobot-Enabled Machine Loading.”
Tell Us What You Think!