Listen to this article
|
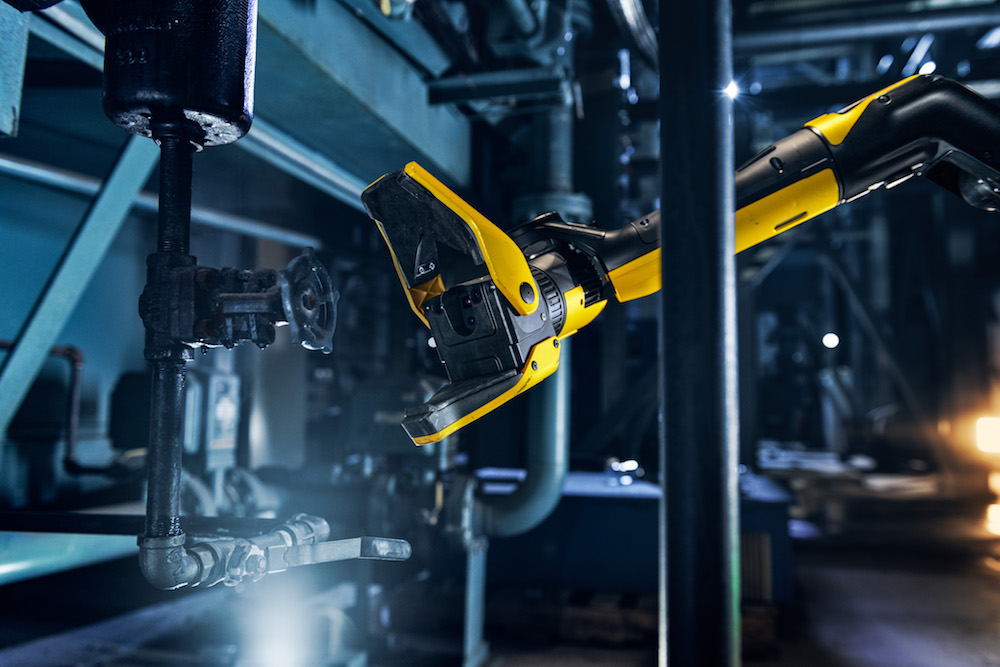
Spot Arm features integrated time of flight, IMU, and 4K RGB sensors. | Credit: Boston Dynamics
Boston Dynamics today released several updates to its Spot product line. The goal is to enhance the quadruped’s ability to autonomously monitor job sites. To do so, the RBR50 company introduced a new version of the robot, Spot Enterprise, the Scout web-based teleoperation platform and its long-awaited Spot Arm.
None of these products is more important than Spot Arm. There are 400-plus Spots out in the world, all of which have essentially been used as data collection platforms. With Spot Arm, Spot is no longer just a data collection robot, but rather a highly-skilled mobile manipulator that can interact with its environment.
Spot Arm
The Spot Arm can grab, lift, place, and drag a variety of objects, including door knobs, tools, and valves. Check out the spec sheet below for details about payloads. Manipulating objects with Spot Arm can be done manually or semi-autonomously via constrained manipulation or “Touch to Grasp.” If you’re controlling Spot on a tablet, for example, users simply touch the object on the screen that they want Spot to manipulate. The robot will then autonomously figure out how to best grasp the object. It works with both the Spot Explorer and Spot Enterprise quadrupeds.
Perhaps the most impressive part here is the planning involved and how Spot uses its entire body to manipulate objects. Whether it’s pushing a lever, opening a door (more on that later) or pulling a cinderblock, Spot Arm grabs the object while the four-legged robot base re-positions itself for better leverage.
“If users want to put together a fully autonomous script of arm behaviors, that’s all available to them,” said Zachary Jackowski, chief engineer, Spot, Boston Dynamics. “All of [Spot Arm’s] features are exposed through an API. With the base robot, we never exposed joint-by-joint control of the legs because it’s not a productive exercise when we’ve written all of the walking control algorithms. But for arm motion planning and complex inverse kinematics that take into account environmental factors, we’ve exposed the control in hopes that some great things come out of it.”
Jackowski said that similar to earlier commercial versions of Spot, the 6-DoF arm and two-finger gripper are targeting innovators and developers. He said there’s not a capable mobile manipulation platform out in the world yet, and that Boston Dynamics will learn a lot from customers who buy arm-equipped Spots. The gripper features integrated time of flight, IMU, and 4K RGB sensors, as well as two accessory ports for power and Gigabit Ethernet. Spot has the same ports.
“We’ve been working on grippers for a long time,” Jackowski said. “We have cabinets full of all sorts of grippers. But we decided our first customer-focused gripper would be a rigid finger gripper. You can do a ton of stuff with a simple 1-DoF gripper. Robotiq has shown us that over and over. If it’s designed correctly, you get the right contours in the gripper and the right materials in the fingers. Robotiq’s grippers are iconic and proof that good work can be done with simple robust grippers.”
“The simpler the gripper, the better off you are,” Jackowski added. “It’s lightweight, strong and damage resistant. It’s at the end of the robot arm, which is the position on the robot most vulnerable to damage. It’s capable of manipulating the objects we’ve found our industrial customers are most interested in – door handles, ball valves, tools on the floor.”
Boston Dynamics released several videos showing off some of Spot Arm’s capabilities. The first that sticks out is Spot opening a door with a round door knob. Boston Dynamics said Spot’s door-opening behavior merely requires the operator to point the robot at the door handle and tell it what side the hinge is on. Spot does the rest, pushing or pulling the door and using its foot to hold the door while it re-grasps the door.
Most robots you’ve seen opening doors are opening doors with ADA-compliant hardware. Push handles or levers are much easier than twisting knobs. Doors and robots have never been friends. In fact, doors were the kryptonite of the robots at the 2015 DARPA Robotics Challenge. And back in 2009, iRobot was working on ChemBot, a shape-shifting robot blob designed to squeeze underneath doors. Spot’s ability to open various types of doors make it viable in a variety of human-centric environments.
Another example that stood out was Spot pulling a concrete block. Jackowski said it impressed him as well because it shows the coordinated dynamics between Spot and Spot Arm.
“It’s using a lot of intelligence about the weight of that object and how its body responds to the center of mass and being able to pull that heavy object,” he said. “The cinderblock is a significant portion of the robot’s weight. The robot is actually going limp when the arm is extended – it is going into singularity to drag the cinderblock around and doing that naturally.”
This isn’t the first time a Boston Dynamics robot has been seeing manipulating cinderblocks. Back in 2013, it produced a video that shows a tethered BigDog throwing a 35-pound cinderblock about 17 feet. Comparing Spot Arm and BigDog’s manipulator show how Boston Dynamics’ approach to dynamic, whole-body manipulation has evolved.
“What gets me most excited is that I’m continuously impressed with how big the world is and how many things people need to do that are really important,” said Jackowski. “A really powerful thing happens when you put a product out there and you let the world happen. A customer could say, ‘Hey, this robot arm is perfect for connecting this dangerous hose in my chemical processing plant. You saved me from exposing someone to a dangerous situation.'”
Jackowski said the demo of Spot digging a hole and planting a tree was inspired by a customer who wants to use robots to plant trees on tree farms. He said this was mostly a scripted behavior where Spot followed a set of instructions to apply a certain amount of force over a certain distance in multiple locations.
“Everything’s important for different reasons,” he said in terms of all the new products. “The arm is our same old thing – a piece of robotics technology that the general community has never had a chance to work with before. We’re introducing it in a way that’s done the Boston Dynamics way. There will be a huge explosion of people figuring out what it’s valuable for and teaching us more about robotic control.”
Spot Enterprise
Boston Dynamics introduced a new version of the quadruped called Spot Enterprise. Essentially, it has all the features of the Spot Explorer base model, but is more autonomous thanks to self-charging capabilities via a docking station, upgraded hardware for improved safety and behavior, more flexible payload ports, post-mission data download and more.
With a push of a button, Spot Enterprise can dock and undock autonomously, but it needs to be within somewhat of a close range to see the docking station’s fiducial marker. Jackowski said they’re working on one-button return to the docking station regardless of where Spot Enterprise is located.
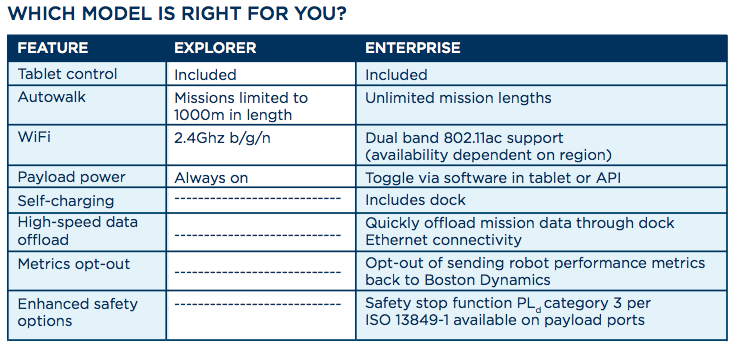
Credit: Boston Dynamics
Scout teleoperation platform
Boston Dynamics also released a teleoperation platform, Scout, that let’s user remotely control Spot. I demoed the platform this morning, walking Spot around Boston Dynamics’ headquarters, going up and down stairs, walking over rocks and inspecting some random gauges. I even managed to topple Spot over, which is no easy task, mind you. Unfortunately, the demo version of Spot wasn’t equipped with Spot Arm.
Yes, there’s a tiny bit of lag. Yes, there’s a learning curve involved to familiarize yourself with the Scout platform. But the “click to go” feature couldn’t make moving Spot around any easier. You literally click a point on the screen and Spot will walk there. You can configure how fast Spot moves, the size of its obstacle avoidance range (down to about 10 centimeters), and quickly scroll through multiple onboard cameras for different angles.
To walk Spot up and down stairs, all I had to do was position the robot in front of the staircase and put it into “Stairs Mode.” Spot does the rest itself. Spot walks down the stairs backwards due to the configuration of its knees. There’s even a “Terrain Mode” that enables users to visualize the sensor data Spot is capturing about its environment. I thought this would be of interest mainly to academics, but Jackowski said industrial users also requested the feature.
“They want to understand exactly what the robot is seeing so that they’re always telling it to do the right thing,” he said. “They don’t want Spot to go somewhere it hasn’t correctly perceived. It’s all about reducing uncertainty in environments where you’re trying to accomplish a task.”

Spot Enterprise comes with the ability to self-charge via this docking station. | Credit: Boston Dynamics
I recently tested a third-party teleoperation platform for Spot from Formant. I walked Spot around Golden Gate Park in San Francisco, controlling it from my home in Massachusetts 3,000-plus miles away. Formant’s platform and Scout are similar in nature, but Jackowski said Boston Dynamics wanted to work on a teleoperation platform itself rather than outsourcing to a third party.
“We’re working with users intensively to find out how they’re finding value and what pieces we need to add to make it a useful tool rather than an interesting one. There’s some really good work in this space, but we’re interested in having a first-party product to integrate deeply with the robot and create user interfaces that show there’s an intelligent robot underneath.”
One of those features could be push notifications to users. For example, if you set Spot’s obstacle avoidance range to be too large, Spot will refuse to go up or down stairs as it’ll think it will bump into the railings. A push notification reminding users to lower the range could be helpful.
While I didn’t test this during the demo, Spot also has a microphone built into its body. Jackowski said this was requested by industrial users. Some use it to capture audio data from pumps and motors to ensure they’re operating properly. We also tested Spot’s thermal camera to ensure the most important application of all – the coffee maker at Boston Dynamics’ Waltham, Mass.-based headquarters was working at full capacity.
Jackowski said a slew of features will be added to Scout over the next year, particularly focused on autonomy.
Boston Dynamics hosted a live event today to go further in depth about these products. You can watch a replay of this event in the video below.
Tell Us What You Think!