Listen to this article
|
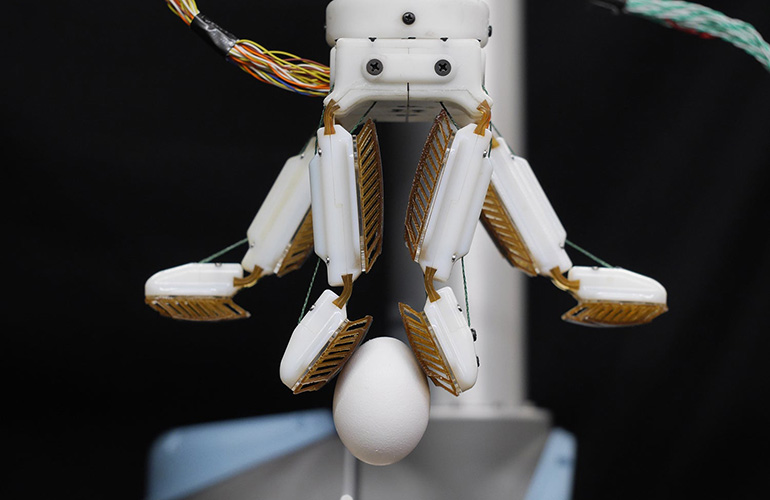
The key to this robotic hand’s grip are at the ends of its fingers. It’s unique adhesive pads help it to grip objects with little force. | Source: Stanford University
Stanford researchers set out to make a robotic hand that can do it all, from picking up delicate objects like raw eggs and tomatoes, to handling large objects like basketballs.
“You’ll see robotic hands do a power grasp and a precision grasp and then kind of imply that they can do everything in between,” said Wilson Ruotolo, PhD ’21, a former graduate student in the Biomimetics and Dextrous Manipulation Lab at Stanford University. “What we wanted to address is how to create manipulators that are both dexterous and strong at the same time.”
Ruotolo and Dane Brouwer, a graduate student in the Biomimetics and Dexterous Manipulation Lab at Stanford, took a unique approach to developing their robotic hand, farmHand.
FarmHand takes inspiration from biology. It’s four, multi-jointed fingers resemble human hands, but the ends of the fingers are covered in gecko-inspired adhesives. The adhesives have been in development for the last decade at the Biomimetics and Dexterous Manipulation Lab, led by Mark Cutkosky.
The material the adhesives are made up of isn’t sticky. Rather, they grip to an object using microscopic flaps that create a Van der Waals force, similar to the toes of geckos. A Van der Waals force is a weak intermolecular force that comes from small differences in the positions of electrons.
The gecko-adhesives are able to grip strongly, with little force, and don’t feel sticky or leave behind a residue. They seem like the perfect answer to the problem, and they’ve been used in similar applications before.
In 2019, OnRobot released an end effector for collaborative robot arms called the Gecko gripper. This gripper used millions of micro-scaled fibillar stalks that adhere using a Van der Waals force. In 2020, the company released a smaller version of the gripper.
“The first applications of the gecko adhesives had to do with climbing robots, climbing people or grasping very large, very smooth objects in space. But we’ve always had it in our minds to use them for more down-to-earth applications,” said Cutkosky. “The problem is that it turns out that gecko adhesives are actually very fussy.”

OnRobot’s Gecko Gripper uses similar technology
The grippers need to connect with a surface in a particular way to work. For example, OnRobot’s end effectors are flat, and can only pick up flat, smooth objects. The grippers are a more environmentally friendly alternative to vacuum end effectors.
There are three principles that the researchers focused on to make the gecko adhesives useful in everyday applications: high contact area, shear load sharing and evenly distributed normal stress.
The researchers found the key to making the adhesives work in the finger pads below the adhesives. The finger pads are made of a collapsible rib structure that buckles under little force. The buckling ensures that there are equal forces on the adhesives.
Another key aspect to the hand are its tendons. Many robotic hands pinch objects in a “C” shape, but farmHand instead hyperextends to make more of a pinching motion. This way, farmHand picks up objects with the pads of it’s fingers pressed together.
To test farmHand, the researchers 3D printed hard and soft plastic components. Typically, researchers would use computer simulations to test different designs, but the researchers had to use other means because existing computer programs are unable to predict real world performance with soft objects.
To further improve farmHand, researchers are exploring feedback features that would help them understand how the hand is gripping and how it can be improved while it’s in use. They are also considering commercial uses for farmHand.
Editor’s Note: The researchers entire study can be found here.
Tell Us What You Think!