Listen to this article
|
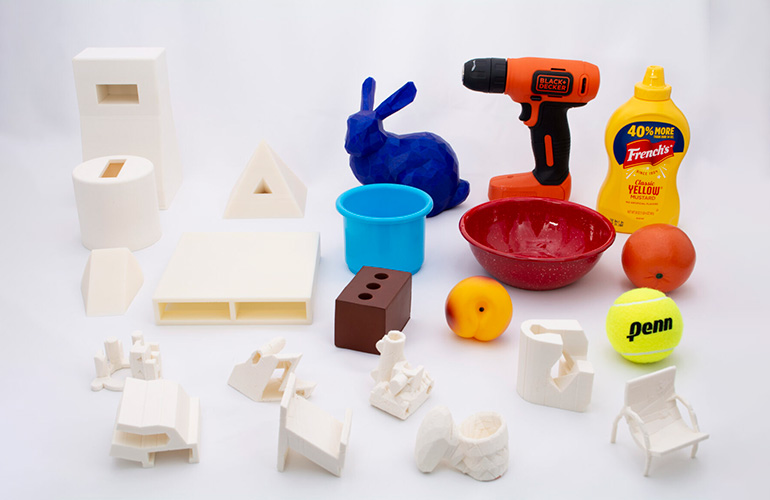
The 22 objects that the University of Washington team tested its grippers on. | Source: University of Washington
Researchers at the University of Washington have developed a tool that can design 3D-printable, passive grippers so that robots can more easily switch between different tasks.
Many robots are tied to a single job and are unable to switch gears if needed to perform a task outside of their usual one. University of Washington researchers are hoping to address this issue by creating a system that can design passive grippers, so the robot can switch out grippers and perform a task with new objects.
To design the grippers, the team provides the computer with a 3D model of the object it’s going to pick and its orientation in space. The team’s algorithms then generate possible grasp configurations and ranks them based on stability and other metrics.
Next, the computer picks the best option and co-optimizes it to see if an insert trajectory is possible. If it can’t find one, it moves on to the next option until it finds one that will. When it does, the computer outputs instructions for a 3D printer to create a gripper, and for the robot arm to find the trajectory for picking up the object.
The researchers tested its system on 22 different objects and successfully picked 20 of them. For each shape, the researchers did 10 pickup tests. For 16 of the shapes, all 10 tests were successful.
The robot was unable to pick two of the objects because of issues in the 3D model of the objects that were given to the computer. The first object, a bowl, was modeled with thinner sides than they really were, and the second object, a cup with an egg-shaped handle, was incorrectly oriented.
The system excelled at picking objects that vary in width or have protruding edges, and struggled with uniformly smooth surfaces, like a water bottle.
The research was funded by the National Science Foundation and a grant form the Murdock Charitable Trust. Authors on the paper include Milin Kodnongbua, Ian Good, Yu Lou, Jeffrey Lipton and Adriana Schulz.
Tell Us What You Think!