Increasing levels of autonomy have led to robotics adoption in multiple industries, but manufacturing has yet to benefit from greater flexibility and ease of use, according to Omnirobotic. The Laval, Quebec-based startup today announced that it has closed a seed round of $6.5 million CAD ($5 million U.S.) to further develop and commercialize its AI platform for factory robots.
“The skills gap in manufacturing is getting worse, as documented by Deloitte and the Manufacturing Institute. In the next decade in the U.S. alone, 2 million jobs will be unfilled that require training, such as welders and machinists,” said Francois Simard, co-founder and CEO of Omnirobotic. “We still need to build bridges or build tractors to grow food. Encapsulating knowhow in a cognitive platform is the only way I know to guarantee this for years to come.”
Simard and Laurier Roy founded Omnirobotic in 2016. The company said businesses have already used its artificial intelligence platform to set goals for robots without needing to program them. The technology can help manufacturers overcome skilled labor shortages, add flexibility to production processes, reduce their environmental impact, and relieve workers of dangerous or unpleasant tasks, it claimed.
Omnirobotic said the funding will enable it to continue building autonomous capabilities for high-mix production environments. It said its systems allow industrial robots to see, plan, and execute high-value-added processes such as painting, welding, and machining with limited human oversight.
Adding autonomy to production
Industrial automation has existed for decades, but adding flexibility to manufacturing has been a challenge. “At university, I was the director of a group of students in a competition for walking autonomous robots,” Simard told The Robot Report. “I started working on machine vision for manufacturing in 2000 and developed 3D perception and self-programming for an award-winning Pratt & Whitney project.”
“Each project we worked on was a custom design, which was difficult and took a long time,” he recalled. “My company at that time was acquired by an integrator working on robotics for structural welding. I worked on self-programming capabilities for six years and met Laurier. We agreed that building autonomous systems could be much faster, simpler, and more powerful.”
“Aside from automotive and consumer electronics, most manufacturers are not mass manufacturers,” Simard said. “For example, with machinery, office furniture, or aerospace — these sectors are making small batches of products, hundreds or thousands of SKUs, which are changing all the time.”
“They need robots to be aware and understand what they’re doing or to figure out painting or machining by themselves,” he added. “It’s a hard challenge, requiring 3D perception, a cognitive platform, and motion planning, all in real time. Omnirobotic will settle for nothing less than a fully autonomous robot.”
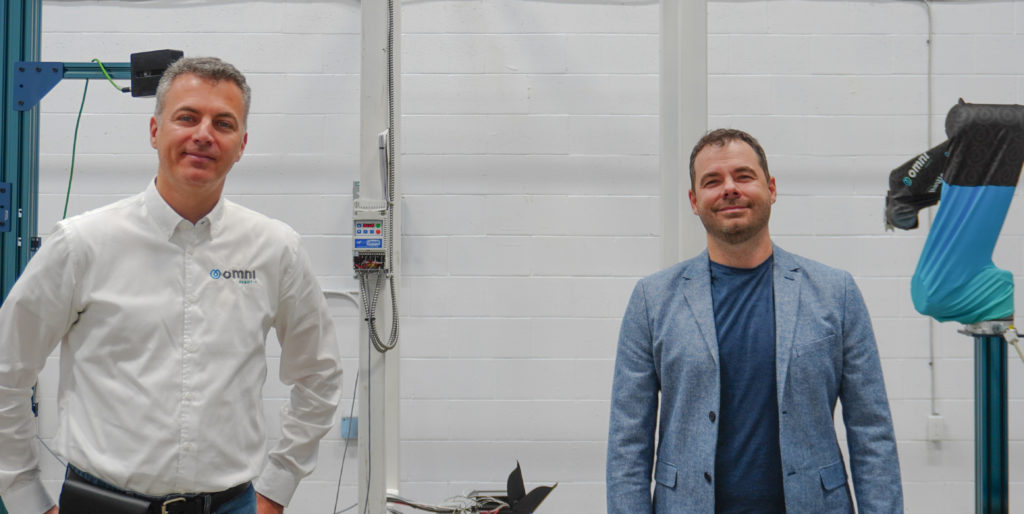
Co-founders Francois Simard, CEO (left), and Laurier Roy, CTO. Source: Omnirobotic
Omnirobotic addresses general industry
“Our typical customers would like to automate a paint operation in the finishing room. Today, they hang parts manually and mix and match by color. Humans are exposed to toxic gases,” Simard said. “We’re convincing customers that they can use robots for that. They’ve been asking robot OEMs how to do this, but they are not used to general industry. They say, ‘Sorry, robots won’t help. There are too many SKUs and no locating jigs.'”
“Then they find Omnirobotic for robots that can figure out how to do the job,” he explained. “We provide the camera platform and perception systems that acquire the 3D shape of any parts and pose or orientation in space. We’ve designed our own Omniscanners, which are designed to be IP67, or submersible and tough enough to be installed on the shop floor.”
“We then figure out the manufacturing steps, which we call creating an execution plan,” said Simard. “Is it feasible? Is there space? There’s a planning conversation happening in our Omnibrain, which runs on our hardware and software somewhere on premises. We select the robot brand and type — usually from a robot OEM or the customer — and we just confirm if it has the reach and capability.”
Omnibrain a ‘cognitive engine’
“In a typical painting line, a wall of parts travels down the finishing department,” Simard said. “The Omnibrain can control one line with one robot on each side. For taller parts, we’ll see a mezzanine, with two workers on each side and on two levels. We want to use the same layout to minimize project costs. One Omnibrain controlling four robot arms makes workload sharing easy.”

A robot arm controlled by AI paints. Source: Omnirobotic
Why not go with cloud computing? “Not many manufacturers are confident enough to run in the cloud,” said Simard. “We install the Omnibrain somewhere cool and dust-free to remotely control robots and get data from 3D cameras. It’s usually 100 to 1,000 feet away, and we run dual lines to the shop floor.”
In terms of flexibility, what’s the difference between Omnibrain and collaborative robots? “You still need to program cobots and teach them step by step, setting every single waypoint in space to achieve a goal,” Simard replied. “Sure, you can program robots faster by programming by pose, but they don’t understand what they’re doing. They would need to analyze a shape for painting and determine where to start. There’s no domain knowledge.”
“With our system, the machine knows how to paint, and it can figure out how to process a new shape, turning that into kinematic motion and so many millimeters of thickness of paint,” he added. “Our cognitive engine and realization plan differentiate us from pretty much any company.”
“Many people think we just put sensors on a human to capture the motion and train the robot, but it’s much more complicated than that,” said Simard. “To make AI understand a goal and allow users to set goals, it must understand process constraints. It searches the solution space in a process similar to finding the shortest route to a destination. Motion planning is like driving autonomously on a road. Sometimes, something unexpected happens, and it needs to replan.”
“We don’t train the robot for many hours or days; the engine is generic, and it’s more about defining goals or using the search engine to find the right motion to do the job,” he said. “We’re not trying to reinvent how to do processes.”
“Omnirobotic is doing for robots what could be done for the transportation industry if you had a startup with 3D sensors and AI to turn any car into a self-driving car,” he said. “We can turn any industrial robot into a self-driving robot that knows what painting or welding is, with the ability to understand an object’s shape and infer the right motions to do the job. We want to empower workers to escape harmful environments and become supervisors for more efficient production.”
Omnirobotic recognized by investors, seeks partners
Fonds de solidarité FTQ and Export Development Canada (EDC) led the round, with participation from Real Ventures and a joint venture including the company’s current employees. The Fonds and EDC recently agreed to work closer together to support Canadian startups, and their joint investment in Omnirobotic is a first in this partnership.
“By bringing new innovative products and services to market, Omnirobotic makes it easier for manufacturers to innovate themselves through a successful technology transition,” stated Janie Béïque, executive vice president for investments at the Fonds. “However, companies such as Omnirobotic need access to venture capital to ensure their growth.”
“In collaboration with institutional investment partners like the Fonds, EDC’s investment Matching Program is enabling Canadian companies to execute on their commercialization and international growth plans in these challenging economic times,” said Carl Burlock, executive vice president and chief business officer at EDC.
Omnirobotic has drivers for robots from the major vendors, including ABB, FANUC, Kawasaki, KUKA, Motoman, and Universal Robots, said Simard. The company is looking to double its staff of 15 robotics and AI experts and to build partnerships.
“We’re raising money to bring the technology to a maturity level and democratize it. We would like integrators and end users to build their own systems using our platform without immediate assistance,” Simard said. “In the next few months, we will also be announcing multiple commercial partnerships focused on targeting currently under-addressed high-mix firms.”
“We started with industrial paint, but paint is just the beginning. Our investors believe in our plan to build the definitive AI platform for Factory Robots,” said Simard. “This won’t just unlock robotics for the entire manufacturing industry, but will also make costly, extensive, painstaking robot programming a thing of the past, paving the way for a new era of autonomous manufacturing.”
Tell Us What You Think!